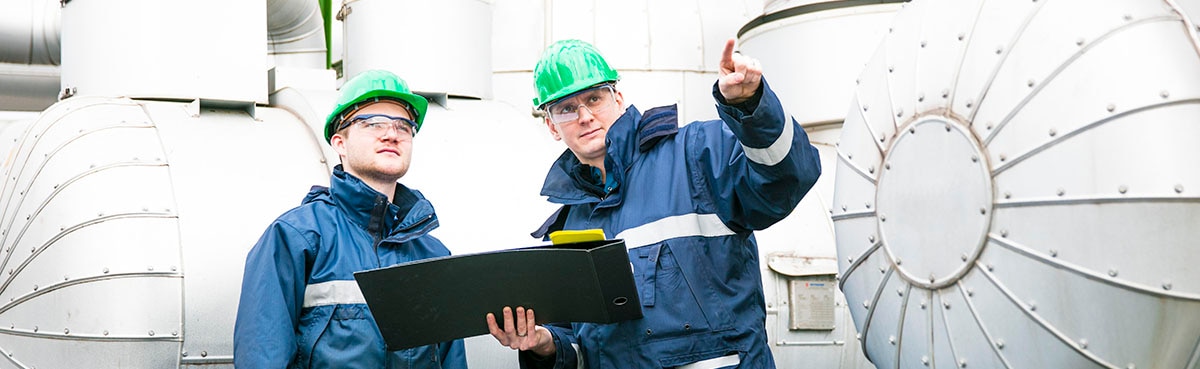
Manufacturing Supervisor
About OQ Chemicals:
OQ Chemicals is a global manufacturer of Oxo Intermediates and Oxo Performance Chemicals with around 1,400 employees worldwide. Our products are used in various applications such as paints and coatings, lubricants and functional fluids, and personal care products.
Bishop, US, 78343
OQ Chemicals Company Overview | World leader in Oxo Chemicals
Oxo products are the core competency of OQ Chemicals. We are producing more than 70 oxo intermediates and oxo derivatives for customers in a wide range of industries with various end market applications. Our chemicals are important ingredients in products that are used in daily life around the world. "We" refers to more than 1,400 OQ Chemicals employees worldwide. At our plants in Germany, the USA, China and the Netherlands, we produce intermediates and derivatives.
Job Purpose:
Provides the leadership and supervision for the Manufacturing team to safely produce high quality products that meets or exceeds customer requirements. Prioritize process and personnel safety while ensuring unit stability, environmental compliance, and effective cost control. Functions include production planning, personnel and team development, maintenance planning and execution, project identification and prioritization, and overseeing management of unit operating budgets. The focus of this position is the safe, efficient operation of the facility.
The position will act in accordance with the Group’s Mission, Vision, Values & Strategies, as well as, policies, guidelines and international standards, supported by an IT Technology platform, HSE standards.
Main Tasks and Responsibilities:
- Supervise the overall direction, coordination, and evaluation of assigned unit personnel, setting the goals and objectives in coordination with Operations leadership team.
- Create and promote a safe, healthy and environmentally friendly atmosphere. Ensures compliance with all relevant HSE regulations and procedures and policies
- Maintains an active and effective safety program. Leads Process Safety efforts for all direct reports. Supports all elements to the Safety Process including Management of Change, Safety Awareness Programs, Environmental Compliance and compliance with policies and procedures.
- Fulfil supervisory responsibilities in accordance with the organization's policies and applicable laws.
- Confer with Operations and QA leadership to establish production and quality control standards.
- Responsible for cost control in Operations Unit.
- Plan and direct production activities and establish production priorities for products in keeping with effective operations, cost factors, and utilization of human resources, machines, and equipment.
- Review OSR, bad actors, production efficiencies and analyze production, quality control, maintenance activities.
- Responsible for the revision of production schedules and priorities as result of equipment failure or operating problems
- Set priorities with manufacturing and technical engineering personnel on unit project initiatives and troubleshooting activities.
- Responsible for coaching to maximize individual employee performance including workmanship, attendance, safety and job performance
- Serve as primary communication vehicle between Operations Leadership team and production employees
- Provide leadership to continuously improve safety, quality and efficiency by the application of Lean Manufacturing principles
- Provide equipment design and process calculations (HTRI, CHEMCAD, etc) support to Project Engineer
- Provide support for site technical requirements including process engineering, design engineering, and other process related calculations
- Monitor and generate Management of Change for activities in the unit
- Responsible for efficient scheduling, staffing, schedule changes and hiring of human resources working with site manager
- Provide support for product loading and scheduling
- Manage Operator Performance Management System (PMS)
- Provide daily instructions and operational changes to Operators
- Responsible for achieving production and raw material efficiency targets
- Provide technical support for environmental reports and calculations for permits
- Provide calculations and technical support for environmental reporting on chemical spills and releases
- Resonsible for reporting raw material and utilities comsumption to management and site partner
LEADERSHIP CORE RESPONSIBILITIES:
- Role models the company core values. Lead, coach and empower employees and teams.
- Develop self-directed teams within the workforce that empower each individual and encourage them to learn new skills creating a flexible workforce
- Effectively communicate both orally and written, demonstrate openness and effective listening
- Facilitate the communication of pertinent information with other teams, departments, functional areas, and other key stakeholders.
- Motivate and challenge to drive high performance
- Hire and provide training for employees and manage personnel issues relating to attendance, vacation scheduling and disciplinary action
- Create an inclusive environment which embraces and derives value from diversity to meet plant and company affirmative action and EEO requirements
- Frequent meeting with team members, management team and other department personnel to develop a positive relationship
- Supporting Operations team by holding team mebers accountable for safety, quality and production.
- Assures employee succession plan is in place
- Execute performance and career development discussion
- Assures employee sucession plan is in place
Key interactions
Internal: Work closely with all Operations Leadership to ensure process needs are met and ensure all process changes are taking place in a timely matter. Coordinate with other departments (HSE, Maintenance, Technical, QA, HR etc.) to ensure optimal performance in Operations.
External: 3rd party contractors and/or vendors as appropriate
Notable Working Conditions: Chemical plant environment and must be able to work long hours not only at the plant but also be able to be reached at night and weekends while at home as well. Must be able to support unit operations not only while unit is running well but during emergencies and upset condition also.
Education Requirements: BS ChE required
Language Requirements: English
Background and Experience:
- BSChE required with 0-5 years work experience
- Excellent Math and Computer skills required
Desired:
- 0-5 years supervisory experience in a manufacturing environment
- Lean Manufacturing/Six Sigma experience
- Process Engineering/Process Control experience
- SAP experience
Competencies and Skills:
- Ability to leverage strong leadership, communication and presentation skills to effectively collaborate with management and employees
- Proficiency with Microsoft products
- Excellent verbal and written communication skills
- Excellent problem solving skills
- Demonstrated ability to lead and influence others
- Able to work flexible hours
OQ Chemicals is proud to be an equal opportunity employer. We do not tolerate discrimination based on race, sex, age, color, national origin, marital status, religion, sexual orientation, gender identity, disability status, veteran status, or any other basis protected by law.
Our Benefits
- Excellent Medical, Dental, and Vision Insurance Plans
- Health Equity Health Fund for health and dependent care
- Disability Benefits
- Basic Group Term Life and Accidental Death and Dismemberment (AD&D)
- Tuition Reimbursement
- Work/Life Balance
- Paid Time Off for a balanced life
- Competitive salary, bonus, 401(k) plan with match and profit-sharing match
Nearest Major Market: Corpus Christi